The use of cyclone separators for the removal of suspended dust particles from gases is discussed in Section 1.6. By suitable choice of operating conditions, it is also possible to
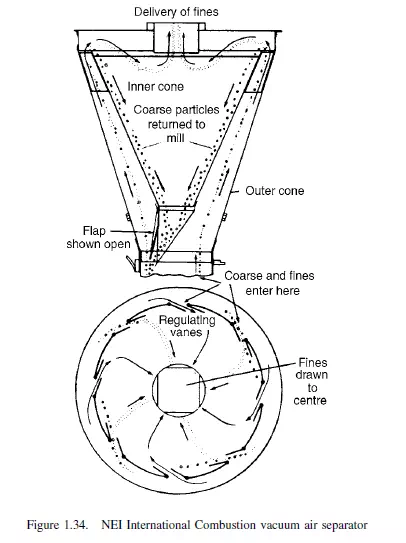
use centrifugal methods for the classification of solid particles according to their terminal falling velocities. Figure 1.34 shows a typical air separation unit which is similar in
construction to the double cone-classifier. The solids are fed to the bottom of the annular space between the cones and are carried upwards in the air stream and enter the inner cone through a series of ports fitted with adjustable vanes. As may be seen in the diagram, the suspension enters approximately tangentially and is therefore subjected to the action of centrifugal force. The coarse solids are thrown outwards against the walls and fall to the bottom under the action of gravity, while the small particles are removed by means of an exhaust fan. This type of separator is widely used for separating the oversize material from the product from a ball mill, and is suitable for materials as fine as 50 μm. A mechanical air separator is shown in Figures 1.35 and 1.36. The material is introduced at the top through the hollow shaft and falls on to the rotating disc which throws it outwards. Very large particles fall into the inner cone and the remainder are lifted by the air current produced by the rotating vanes above the disc. Because a rotary motion has been imparted to the air stream, the coarser particles are thrown to the walls of the inner cone and, together with the very large particles, are withdrawn from the bottom. The fine
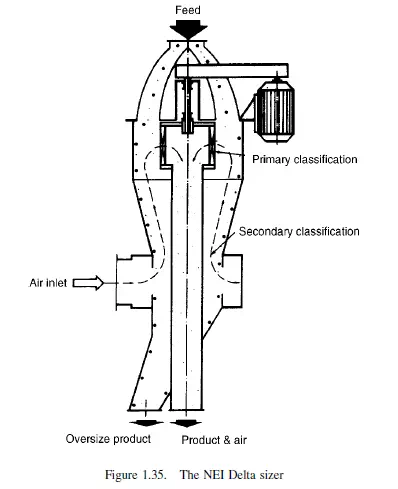
particles remain in suspension and are carried down the space between the two cones and are collected from the bottom of the outer cone. The air returns to the inner cone through a series of deflector vanes, and blows any fines from the surfaces of the larger particles as they fall. The size at which the “cut” is made is controlled by the number of fixed and rotating blades, and the speed of rotation. The Delta sizer is designed to separate dry powders of mixed particle size within the range 5 to 200 μm into distinct fractions at a high extraction efficiency and low power consumption. The equipment shown in Figure 1.36 has a feed rate from 2 to 7 kg/s depending upon the desired cut point and the bulk density of the material.