The importance of chlorinated organic compounds in the field of agrochemicals and pharmaceuticals is comparable to that for organofluorines regarding improved pharmacological properties. In addition, chlorinated compounds are useful building blocks for the generation of more complex structures, as well as for the preparation of plastic materials or dyes.40
One of the most widely utilized procedures for the generation of organochlorines is the transformation of alcohols into the corresponding chlorides by substitution of the OH group. Chlorinating reagents such as SOCl2 or PCl5 are often used for this reaction. The greenest alternative for these chlorodehydroxylation reactions is the use of HCl as reagent, as demonstrated by the group of Hessel.41 Using directly anhydrous HCl gas, the neat alcohols were converted into the corresponding chlorides at 120 °C and 10 bar pressure (Scheme 5). Special precautions had to be taken to keep the HCl dosing part of the system anhydrous, as moisture in the HCl produced significant damage of metal parts such as the mass flow controller. In a previous work the use of aqueous concentrated HCl instead of the gas had been demonstrated as a suitable alternative,42 although a larger excess of HCl (3 equiv.) was required.
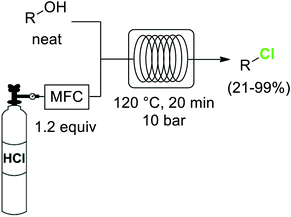
Scheme 5 Conversion of alcohols to chlorides using HCl gas.
Elemental chlorine (Cl2) is a powerful and atom-economic chlorinating agent for organic compounds, as well as one of the cheapest oxidizing agents available.43,44Despite the importance of Cl2 as an oxidizing and chlorinating agent in organic synthesis, its extremely high reactivity limits its use in many instances, as undesired overreactions and exotherms typically occur. The efficient mixing and enhanced mass transfer achieved under continuous flow conditions minimize these problems. Moreover, the small channel dimensions in a microreactor are a key advantage in the case of photochlorination reactions, where intense and uniform irradiation of the reaction mixture is required. This was demonstrated by the pioneering work of the group of Jähnisch,45 where a falling film microreactor was used to carry out the gas/liquid reaction of toluene-2,3-diiocyanate (8) with Cl2 under UV irradiation (Scheme 6a). The falling film reactor was equipped with a quartz window (Scheme 6b) and a 1000 W xenon lamp (190–250 nm). Compared to batch mode higher selectivity for the desired benzyl chloride 9 was obtained. The space-time yield achieved in flow (400 mol L−1 h−1) was also much higher than in batch (1.3 mol L−1 h−1) due to the small reaction volume and short residence time required. A similar strategy was used by the group of Ryu for the radical chlorination of cycloalkanes.46 The microreactor consisted of stainless steel microchannels covered by a Pyrex glass window, that was irradiated with a 15 W black light CFL. The neat cycloalkanes were introduced into the reactor using a syringe pump. A moderate yield (20%) was obtained for the generation of chlorocyclohexane. Alternatively, SO2Cl2 was used as chlorine source.46 In this case a solution of the reagent in the corresponding cycloalkane was directly pumped through the microreactor (Scheme 6c) under the same conditions. Plug flow derived from the release of SO2 could be suppressed by installing a back pressure regulator at the end of the flow setup.
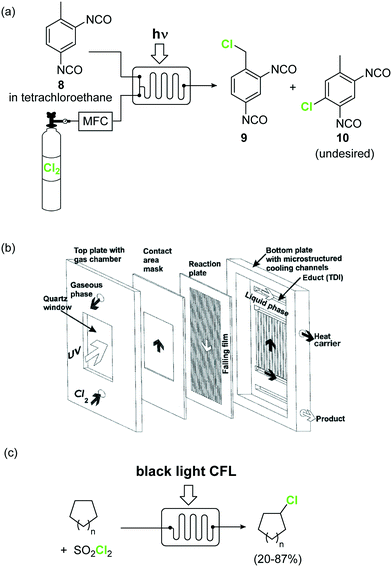
Scheme 6 Photochemical chlorinations using Cl2 gas. Image 6b reproduced with permission from ref. 45: H. Ehrich, D. Linke, K. Morgenschweis, M. Baerns and K. Jähnisch, Chimia, 2002, 56, 647–653. Copyright© 2002 Swiss Chemical Society.
Apart from the problems associated with the high reactivity of Cl2 towards organic compounds, handling and storage of Cl2 gas cylinders in organic synthesis labs and production facilities is an important safety issue on his own.47 Use, handling, and transportation regulations for this substance are strictly regulated. Sites where Cl2 gas is used normally need to be isolated, and the personnel specifically equipped and trained for the handling of chlorine.47 To solve this problems a continuous flow generator of Cl2 based on the reaction of NaOCl and HCl was developed.48 The simple continuous flow setup consisted of three peristaltic pumps (Vapourtec E-Series) that pumped aqueous solutions of NaOCl and HCl, in addition to CHCl3 (Scheme 7). Upon mixing of the aqueous solutions, Cl2 gas was rapidly formed and extracted to the CHCl3 phase. A hydrophobic membrane based continuous liquid–liquid separator was then used to separate the organic phase containing Cl2 in solution from the aqueous phase. A yield of 90% based on NaOCl was obtained.48 The chlorine generator was tested for several organic reactions, including the selective oxidation of primary alcohols using the chlorine–pyridine complex, and the chlorination of silanes and benzylic compounds. For the photochemical chlorination of benzylic compound the Cl2 solution in CHCl3 obtained from the membrane separator was mixed with the neat toluene derivative (Scheme 7) before entering a photoreactor equipped with a Hg lamp (150 W). After a residence time in the photoreactor of ca. 15 min the reaction mixture was quenched at the reactor output with isopropanol. Excellent yields were obtained for several benzyl chlorides. NaOCl has also been used directly for the continuous chlorination of amines.49
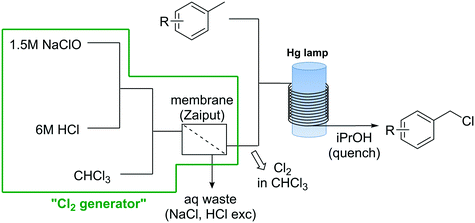
Scheme 7 Photochemical chlorination of toluene derivatives with in situ generated Cl2.