Abstract
The halogenation of organic substrates is one the most important transformations in organic synthesis. The most straightforward, inexpensive and atom economic halogenations involve the use of elemental halogens (X2) or hydrogen halides (HX). However, X2 and HX reagents are highly reactive, toxic and corrosive materials. Halogenations using these reagents are usually very fast and exothermic reactions, in which selectivity issues occur. Using continuous flow chemistry halogenations involving X2 and HX can be performed in a safe and controllable manner. Reagents can be accurately dosed even for gas/liquid reactions, and exotherms are easily controlled. Hazardous chemicals can be readily quenched in line avoiding any undesired exposures and significantly enhancing the process safety.
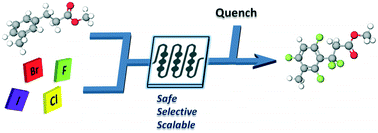
Introduction
The introduction of one or more halogen atoms into organic molecules is arguably one of the most important and often required transformations in organic synthesis.1,2Halogenated compounds constitute ca. 20% of the repertory of active pharmaceutical ingredients (APIs), and 30% of current agrochemicals.3 Halogenated compounds also find applications as dyes, flame retardants, imaging agents in medical diagnosis, and in materials science.1–3 The significance of halogenated compounds is increasing rapidly. Thus, ca. 80% of newly developed agrochemicals during the first decade of the 21st century contained one or more halogen atoms.3 Notably, 7 out of the top-10 best-selling drugs in the US in 2014 were halogenated compounds (some examples are shown in Fig. 1).4 Almost 5000 naturally occurring organic halogenated compounds have been identified so far.5 The beneficial effects of a carbon–halogen bonds within the structure of organic compounds, such as increased durability, stability towards biodegradation and oxidation, and higher biological activity and membrane permeability, are shared by synthetic APIs and natural compound.6,7 A notable difference is the relative distribution of the halogen elements among synthetic and naturally occurring organic compounds (Fig. 2). While chlorinated and brominated derivatives predominate in natural metabolites, with a relatively small number of compounds containing fluorine and iodine, synthetic APIs and agrochemicals with fluorine and chlorine are more abundant.3,8 Despite the high incidence of chlorine and fluorine atoms in the final structure of APIs, brominations and iodinations are very often carried out for the generation of synthetic intermediates.9 Halogenated building blocks have seen increased relevance owing to the development of cross-coupling chemistry over the past four decades.10
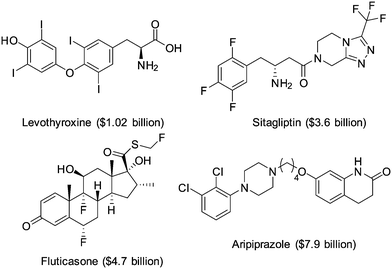
Fig. 1 Examples of halogen compounds ranked among the top-10 selling drugs in the US in 2014. Sales are shown in brackets.
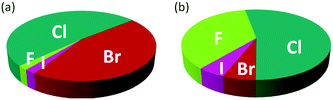
Fig. 2 Distribution of halogens within the structure of naturally occurring compounds (a) and synthetic APIs and agrochemicals (b).
Unlike biochemical processes that use relatively harmless anionic species (e.g. Cl−, Br−) as halogen sources for the halogenation of organic compounds, normally via an oxyhalogenation pathway,11 organic chemists usually employ highly reactive, toxic, and corrosive reagents to carry out halogenation reactions.1,2 Elemental halogens (X2) and hydrogen halides (HX) are the most convenient halogenating agents from the viewpoint of atom economy and simplicity. However, the highly corrosive and toxic nature of these reagents, as well as their high reactivity, are important drawbacks for their use in organic synthesis. Many examples of less reactive, easy to handle halogenating agents have been developed to avoid the use of X2 and HX reagents.12Popular examples are N-bromosuccinimide (NBS) as a substituent of Br2, or the N-fluorobenzenesulfonimide (NFSI) and diethylaminosulfur trifluoride (DAST) fluorinating agents. Yet, preparation of these reagents ultimately requires the use of the corresponding elemental halogen or other highly reactive species.
During the past decade continuous flow- and microreactor technology have been shown to be powerful tools for the safe and controllable use of hazardous or highly reactive reagents in organic synthesis.13–16 The small channel dimensions characteristic of microreactors ensure a very high heat exchange efficiency that suppresses the formation of hotspots, temperature gradients or accumulation of heat.17 Thus, high reaction selectivity and enhanced safety can be achieved even for very fast and highly exothermic reactions. The excellent heat and mass transfer characteristics of microreactors, together with the fact that the reaction is resolved along the length of the reaction channel, enables a precise control of the residence time of intermediates or products by a thermal or chemical quench of the solution.18Highly reactive, toxic, or explosive intermediates can be generated in situ and consumed within the reactor channel by combining multiple reagent streams. Thus, syntheses that were previously “forbidden” due to safety reasons or even reactions simply not possible in batch are possible to handle in a safe and controllable manner.16
Not surprisingly, during the past years the above mentioned benefits of continuous flow and microreactor technology have been applied to many halogenation reactions, were toxic and highly reactive reagents are usually utilized. Halogenations, especially fluorinations and chlorinations, where selectivity is a major issue in batch have especially benefited from the exceptional heat and mass transfer achievable under continuous flow conditions. Improved mixing and mass transfer efficiency in gas/liquid biphasic reactions utilizing F2 or Cl2 as halogenation reagents, or photochemical halogenations where the small channel dimensions of flow reactors ensure intense and uniform irradiation, are examples where translating a process from batch to flow substantially improves reaction efficiency and selectivity, as well as process safety.
Review articles focusing entirely on fluorinations in flow have been published in the past years.19,20 An early survey of the literature on fluorinations, chlorinations, and brominations in microreactors covering the literature until 2004 was published by the Hessel group.21 The current review analyzes the literature on continuous flow halogenations published during the past two decades, essentially from the flourish of microreactor technology at the beginning of the 2000s. Examples in which continuous flow technology has been successfully applied to halogenation reactions difficult to perform under classical batch conditions are described, emphasizing those cases dealing with highly reactive reagents or very exothermic reactions where batch protocols would be practically “forbidden” on industrial scale.