Abstract
Continuous handling of solids creates challenges for realizing continuous production of pharmaceuticals and fine chemicals. We present a new miniature continuous stirred-tank reactor (CSTR) cascade to handle solid-forming reactions in flow. Single-phase residence time distribution (RTD) measurements of the CSTR cascade reveal nearly ideal CSTR mixing behavior of the individual units. Consistency of experimental and predicted conversions of a Diels–Alder reaction further confirms the CSTR performance. Two solid-forming reactions, (i) glyoxal reacting with cyclohexylamine to form N,N′-dicyclohexylethylenediimine, (ii) sulfonylation of 2-octanol with methanesulfonyl chloride, demonstrate the ability of the reactor cascade to transport solid particles continuously for hours without significant signs of clogging.
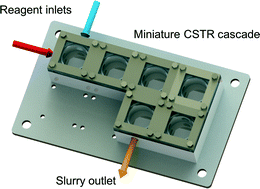
Introduction
Continuous-flow production is the basis of the petrochemical and bulk chemicals industry, where environmental and safety regulations, competition, and long development time drive high-performing, cost-effective, safe, and atom-efficient continuous chemical processes.1 However, the diversity and complexity of fine chemical molecules combined with relatively small annual production leave continuous-flow processes relatively less developed in the pharmaceutical industry.2
Currently, the production of fine chemicals, such as active pharmaceutical ingredients (APIs), typically relies on batch or semi-batch processes. The flexibility and versatility of the batch vessel reduce the investment and time cost of new equipment development for accommodation to different reaction kinetics.3 A survey conducted at Lonza3 analyzed 86 different reactions in the pharmaceutical industry and concluded that 50% of the reactions would benefit from transferring to continuous production. Compared to batch or semi-batch production, continuous production has the advantages of steady state operation, high heat and mass transfer rates, reproducibility, and improved safety and process reliability.4 In the past decade, a large number of single and multistep reactions have been demonstrated as continuous processes.1,5–12
Handling of solid compounds in flow systems without clogging remains a challenge. Numerous important reactions in the pharmaceutical industry involve stoichiometric amounts of solids, which can be present as reagents, intermediates, by-products or products. Large-scale continuous transport of solid particles, such as flow of suspensions in pipelines, is a well-studied area.13–15 In centimeter- or meter-scale tubes, the particle–fluid interactions generated by turbulent flow balance the effect of gravity to prevent settling of particles in the pipe. Below a critical deposit velocity of the fluid, a stationary bed of particles will form on the bottom of the pipe. Due to the complexity of the slurry system, researchers have extensively studied numerous empirical equations for predicting the critical deposit velocity.16
With the laminar flow characteristic of micro- and milli-reactors, particle–wall and particle–particle interactions become important in controlling the behavior of particles in flow. The constriction of particles on the wall caused by particle–wall interaction and agglomeration and the bridging of particles caused by particle–particle interaction make the small-scale transport of slurry more difficult than that on larger scales.17,18
Researchers have proposed innovative methods to avoid solid clogging in flow reactors. For example, Poe et al. used “droplet reactors,” travelling in the carrier phase, to confine solid particles in liquid droplets, thus keeping them away from the tube wall and preventing clogging of the tube reactor.19 Exerting non-contact external forces on particles, such as acoustic,20–23 magnetic,24–26 and electrophoretic forces,27,28 has been used to keep solid particles suspended in the flowing fluid. Application of ultrasonic irradiation to a tube reactor breaks apart agglomerates, which reduces particle sizes and minimizes the chances of forming channel-spanning agglomerates plugging the flow tube.20 Sonication effectively extends the operation time of the tube reactor compared to the scenario without sonication, but scaling of ultrasound has challenges.
Agitated millireactors have been developed for handling solids. Ley et al. used the Coflore ACR agitated cell reactor to demonstrate the continuous formation of the hydroiodide salt of N-iodomorpholine through the reaction of morpholine with iodine29 and built a back pressure regulator to accommodate superheated conditions for slurry-forming reactions.30 Recently, Baxendale et al. realized kg-quantity continuous production of triacetic acid lactone solid, a building block as part of a synthesis program preparing bromodomain-containing protein modulators.31 Solid-producing reactions have also been run successfully with the multijet oscillating disc (MJOD) millireactor that oscillates a multijet disk assembly forward and backward in the longitudinal direction inside a tubular reactor.32,33 Cascades of continuous stirred-tank reactors (CSTRs) are used in the pharmaceutical industry for continuous crystallization in so-called continuous mixed suspension, mixed product removal (MSMPR) crystallizers,34–37 but the liquid hold-up in these systems is often too large (liters) for small-scale organic synthesis.
In the present work, we describe a cascade of miniature continuous stirred-tank reactors (CSTRs) for reactions involving solids. We characterize the single-phase mixing properties of the miniature CSTR cascade relative to ideal CSTR performance. In addition, two examples that generate solids as products and by-products during the reaction serve to assess the ability of the reactor to handle solids continuously.
Comments are closed