In Dryers In dryers, inlet humidity is a controlled parameter which affects the process, whereas outlet humidity is a monitoring parameter which is affected by the process. Inlet humidity Variations in inlet humidity will naturally occur as the ambient conditions fluctuate, with day/night and winter/summer variations. For high drying temperatures (e.g. 1500 C or above) the effect on drying is generally small. However, at the lower temperatures (less than 1000 C) used for temperature-sensitive materials, such as foods and pharmaceuticals, changes in inlet humidity significantly affect the wet-bulb temperature (and hence driving forces and drying times), and the exhaust humidity (influencing product moisture content). Therefore, inlet humidity control must be considered, with the following options: – No control. If the effect on the drying process is unimportant. – Capping. A chilled water coil is used to ensure the inlet dewpoint is no higher than a certain value, e.g. 100 C (7-8 g/kg). – Dehumidification. If very dry air is needed for moisture-sensitive materials, a chemical absorption wheel can be used to give humidities of 2 g/kg or less. – Rehumidification. If the product could dry out too fast or too far, steam or water injection can be used to increase humidity. High humidities can also be achieved by recycling exhaust air. For example, when drying leather in tunnel dryers, air recycle is used to maintain relative humidity in the circuit at 40-50% at temperatures of 40-80o C. Leather cracks and denatures if dried too far, and these conditions keep the equilibrium moisture content at about 15% and prevent further drying. To control humidity within a tight range (e.g. 5 to 8 g/kg), a combination of capping and rehumidification can be used.
Exhaust humidity
Outlet humidity is a good indicator of the progress of drying. For continuous drying, exhaust humidity monitoring shows whether drying is consistent, and can give early warning of fluctuations in solids inlet moisture content or mass flowrate (which can be difficult to measure accurately on-line). For batch drying, exhaust humidity can give an indirect measure of how close the solids are to their desired final moisture content (endpoint). Outlet moisture content is a key part of the dryer product specification, and ideally should be measured on-line. For continuous dryers, this can be done using near infra-red on the product stream, but batch dryers present a greater problem. In-vessel measurements suffer from fouling and non-uniform solids mixing. Hence product moisture is normally deduced from indirect measurements. Product or exhaust gas temperature are normally used as indicators of the endpoint, but exhaust humidity provides a useful alternative or additional information. Figure 2 shows results from a drying kinetics rig at SPS, Harwell, where the outlet humidity was monitored using a fast-response spectroscopic infra-red gas analyser. A mass balance over the dryer module is used to convert humidity to evaporation rate from the solids, giving Figure 3. Then, integration over time gives the drying curve (moisture content variation with time), Figure 4. Note that the integration smoothes out the scatter on the humidity data. However, the result is sensitive to errors in flowrate and humidity measurement, so it is essential to cross-check the drying curve with the initial and final solids moisture contents obtained from an accurate laboratory method, usually an oven test. The mass balance should agree to within 5%.
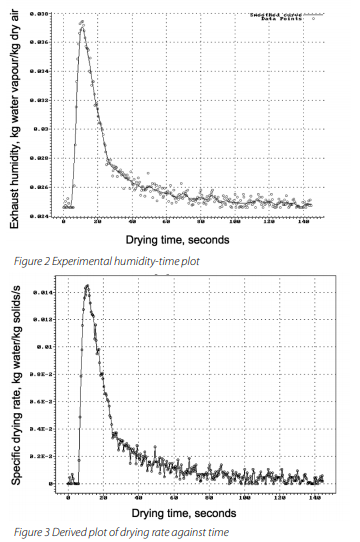
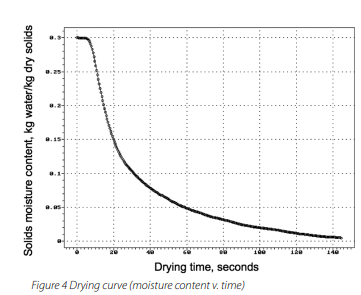