Catalysis is a term coined by Baron J. J. Berzelius in 1835 to describe the property of substances that facilitate chemical reactions without being consumed in them. A broad definition of catalysis also allows for materials that slow the rate of a reaction. Whereas catalysts can greatly affect the rate of a reaction, the equilibrium composition of reactants and products is still determined solely by thermodynamics.
Heterogeneous catalysts are distinguished from homogeneous catalysts by the different phases present during reaction. Homogeneous catalysts are present in the same phase as reactants and products, usually liquid, while heterogeneous catalysts are present in a different phase, usually solid. The main advantage of using a heterogeneous catalyst is the relative ease of catalyst separation from the product stream that aids in the creation of continuous chemical processes.
Additionally, heterogeneous catalysts are typically more tolerant of extreme operating conditions than their homogeneous analogues. A heterogeneous catalytic reaction involves adsorption of reactants from a fluid phase onto a solid surface, surface reaction of adsorbed species, and desorption of products into the fluid phase. Clearly, the presence of a catalyst provides an alternative sequence of elementary steps to accomplish the desired chemical reaction from that in its absence.
If the energy barriers of the catalytic path are much lower than the barrier(s) of the noncatalytic path, significant enhancements in the reaction rate can be realized by use of a catalyst. This concept has already been introduced in the previous chapter with regard to the CI catalyzed decomposition of ozone (Figure 4.1.2) and enzyme-catalyzed conversion of substrate (Figure 4.2.4). A similar reaction profile can be constructed with a heterogeneous catalytic reaction. For example, G. Ertl (Catalysis: Science and Technology, 1. R. Anderson and M. Boudart, Eds., vol. 4, Springer-Verlag, Berlin, 1983, p. 245) proposed the thermochemical kinetic profile depicted in Figure 5.1.1 for the platinum-catalyzed oxidation of carbon monoxide according to the overall reaction CO + ยฑO2 =} CO2, The first step in the profile represents the adsorption of carbon monoxide and
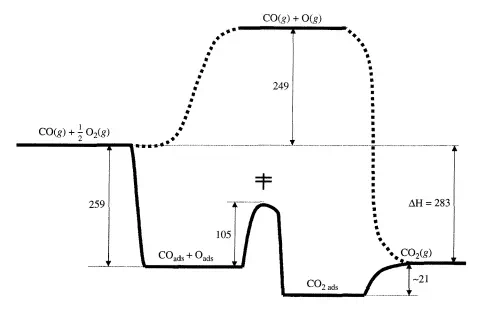
dioxygen onto the catalyst. In this case, adsorption of dioxygen involves dissociation into individual oxygen atoms on the Pt surface. The product is formed by addition of an adsorbed oxygen atom (Oads) to an adsorbed carbon monoxide molecule (COads)’ The final step in the catalytic reaction is desorption of adsorbed carbon dioxide (C02ads) into the gas phase. The Pt catalyst facilitates the reaction by providing a low energy path to dissociate dioxygen and form the product. The noncatalytic route depicted in Figure 5.1.1 is extremely slow at normal temperatures due to the stability of dioxygen molecules.
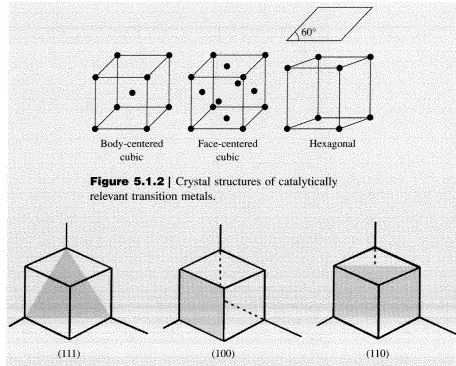
Since the number of atoms on the surface of a bulk metal or metal oxide is extremely small compared to the number of atoms in the interior, bulk materials are often too costly to use in a catalytic process. One way to increase the effective surface area of a valuable catalytic material like a transition metal is to disperse it on a support. Figure 5.1.5 illustrates how Rh metal appears when it is supported as nanometer size crystallites on a silica carrier. High-resolution transmission electron microscopy reveals that metal crystallites, even as small as 10 nm, often expose the common low-index faces commonly associated with single crystals. However, the surface to volume ratio of the supported particles is many orders of magnitude higher than an equivalent amount of bulk metal. In fact, it is not uncommon to use catalysts with I nm sized metal particles where nearly every atom can be exposed to the reaction environment.