Of paramount importance for performing any process at scale is to establish safe operational conditions. Invariably, aerobic oxidation reactions involve a combination of oxygen with flammable materials under high temperature and pressure. This warrants extensive risk assessment to identify safe reaction conditions and apparatus, as well as special measures in case of catastrophic failure. In this section, the specific hazards associated with aerobic oxidations are highlighted.
Reaction exotherm
In general, aerobic oxidations are highly exothermic. For example, the oxidation of benzyl alcohol to benzaldehyde by molecular oxygen generates a net heat of reaction of −187 kJ mol−1 (calculated based on the standard enthalpy of formation of each species).32 As such, these reactions are associated with a considerable adiabatic temperature rise, which needs to be considered for safe operation. Effective management of the heat released from the reaction is vital for any scale-up process. Therefore, it is often advantageous to perform aerobic oxidations in continuous flow, as the internal volume of the reaction system is limited and thus allows better heat dissipation (through the reactor wall) for safer operation.
The inability to efficiently remove the reaction heat can lead to explosive chemical reactions, and their theoretical description is addressed in the seminal works of Semenov33 and Frank-Kamenetskii.34 The underlying basis of both theories is that the ignition of a reactive mixture is attributed to the fact that the production rate of heat (i.e. the net heat of reaction) is larger compared to the dissipation rate of heat (i.e. heat transfer to the ambient). This imbalance will lead to an unsteady thermal state, which will finally cause a reaction mixture to exceed its autoignition temperature and spontaneously combust (see section 3.2).
The theory of Semenov assumes a well-mixed reaction medium, with no spatial gradients in temperature or chemical composition in the reactor. Heat transfer to the ambient is then described via a (uniform) heat transfer coefficient applied as boundary condition on the vessel wall. However, this assumption of a well-mixed reaction medium does not hold for large reactors or heterogeneous reactions. As an extension of the original Semenov theory, Frank-Kamenetskii included the effect of developing temperature gradients and introduced thermal conduction in the reaction medium as main source of heat transfer (assuming a constant reactor wall temperature). Based on the steady-state energy conservation equation, balancing the heat produced from the reaction with the heat removed via conduction, the dimensionless parameter δ can be derived:(1)with the following variables:
hP, hF enthalpies of the product (P) and feed (F)
λ thermal conductivity of the reaction mixture
ρ density of the reaction mixture
L characteristic dimension of the reactor
A pre-exponential factor
EA activation energy
TW wall temperature
From the energy conservation equation, a critical value δcrit can be derived, which is geometry-dependent, e.g. δcrit = 2.0 for an infinite cylinder.34 It follows that no explosion occurs as long as δ < δcrit. Hence, the Frank-Kamenetskii theory can be used to calculate the maximum tolerable wall temperature for different vessel geometries and vessel sizes L when the reaction mixture properties are known.
Both the Semenov and Frank-Kamenetskii theories can provide guidelines for the temperature management of a reactor vessel to ensure safe operation. However, their predictions always need to be evaluated against their underlying assumptions, particularly in terms of the dominating heat transfer mechanism and temperature independent reaction mixture properties. Most importantly, for continuous flow operation, e.g. in packed-bed reactors, heat transfer via convection will dominate, and one would need to extend the theories to account for this.
Flash point, autoignition and limiting oxygen concentration
When the concentration of an organic solvent is within the flammability limits, it can ignite in the presence of O2. This can be avoided by operating below the limiting oxygen concentration (LOC), defined as the concentration of O2 below which a fuel-oxidant explosion cannot occur.35 By limiting the O2 concentration below this value, combustion cannot occur irrespective of the concentration of the organic solvent. It is also important to note that these limiting concentrations are linked to the process temperature and pressure: for each 100 °C increase, the lower flammable limits and the LOCs at 1 atm decrease by about 8% of their values at near normal room temperature; the upper flammable limits increase by approximately 8% for the same conditions.35 The US National Fire Protection Association (NFPA) has provided some guidelines for recommended safety margins.36 For LOCs of ≥5%, the O2 concentration should not exceed 60% of the LOC, but with continuous monitoring the O2 may be kept 2% below the LOC.
Quantification of the LOC requires the detailed knowledge of the flammability region as a function of the fuel, oxidant, and (if present) inert gas concentrations.37 The flammability limits and the LOC can be graphically represented in a flammability diagram, which for the case of the presence of fuel/oxidant/inert will be triangular, but can also be represented in orthogonal shape omitting e.g. the inert concentration as it can be calculated from the mass balance (the sum of all molar fractions equals 1). Using such a diagram allows to determine if a flammability risk exists for the given process conditions. However, it has to be noted that each diagram needs to be constructed experimentally, and is only valid for a certain temperature and pressure.
Furthermore, it is important to note that mixtures of a flammable material and O2can spontaneously combust without an ignition source, as long as the external temperature is enough to attain the required activation energy (‘thermal ignition’ or ‘autoignition’). The autoignition temperature (AIT) must not be confused with the flash point of the solvent (the lowest temperature at which the vapour will form a combustible mixture with air). Some AITs and flash points of selected organic solvents commonly used in the academic laboratory and industrial processes are listed in Table 1.38 It is important to note that these values are recorded at ambient conditions, and will change substantially at elevated temperatures and pressures. For example, while no flash point is recorded for dichloromethane, it is able to form a flammable mixture with air when heated above 100 °C. Similarly, AIT can be lowered substantially by pressure39 and the size of the reaction vessel;40 these issues must be considered in designing scale-up processes for aerobic oxidation reactions.
Many industrial processes are conducted at elevated pressure; for liquid-phase aerobic oxidation reactions, pressure is commonly applied to increase the availability of dissolved oxygen. Given that AIT is an inverse function of pressure, it is important to predict the AIT depression as a function of pressure. For several hydrocarbons, this relationship may be represented by the following equation:41(2)where:
Pc and T0 = initial pressure and temperature at the critical condition;
EA = activation energy of the reaction;
R = universal gas constant; and
C = a constant that includes different factors such as surface/volume ratio of the reaction vessel and heat transfer coefficient.
Critically, this relationship is only applicable over a limited pressure range, since the activation energy is also a function of pressure and temperature. This means that, in reality, the functional relationship between AIT and pressure/reaction temperature needs to be determined experimentally. This is particularly relevant in terms of risk assessment for aerobic oxidation reactions, as the application of O2 pressure is desirable, but reliance on standard measurements of autoignition temperatures is not advisable.
When dealing with gaseous mixtures of organic compounds, AIT can be predicted assuming an ideal mixture contribution method:42(3)where AITi is the component autoignition temperature and Xi is the mole fraction of component i in mixture.
This may be used to predict the AIT of the gaseous mixtures at the reactor exit (particularly in the context of flow chemistry). For the headspace in a batch reactor, the composition of the vapour phase above the reaction mixture and the relative volatilities of the liquid phase must also be taken into account.
Experimental data are very hard to find that show the AIT as a function of temperature or oxygen partial pressure for that matter. Modelling approaches exist for commonly encountered fuels, with the involved model parameters fitted to experimental data and thus also limited to certain process conditions.39 Some of the available data for a number of solvents40 are plotted in Fig. 2 for aerobic oxidation reactions. In this figure, the AIT of various compounds is plotted as a function of air pressure ranging from 1 to 10 bar. The data obey a Semenov analysis (see eqn (2)) but it is clear that different chemical structures will exhibit different gradients (or EA). Nevertheless, we can conclude that at useful operating pressures, i.e. 10 bar (in terms of oxygen solubility) most solvent will exhibit an AIT of around 200 °C. This is concerning, as high pressures will no doubt reduce this temperature even further, thus moving the AIT into the realm of desirable reaction temperatures leading to heightened risks, unless headspace and exit mixture composition can be adequately controlled.
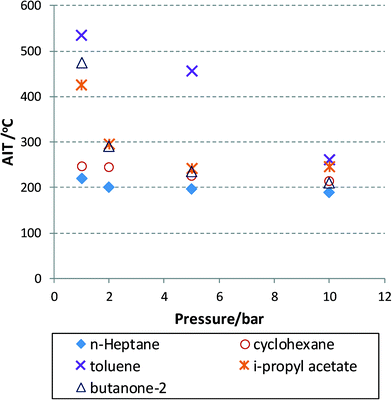
Fig. 2 AIT for mixtures of flammable liquids with air at elevated pressures (air).
Currently, a priori prediction of LOCs is difficult, as it is limited by available experimental data. In a recent publication,30 the LOCs of 9 organic solvents commonly employed in the pharmaceutical industry (acetic acid, N-methylpyrrolidone, dimethyl sulfoxide, tert-amyl alcohol, ethyl acetate, 2-methyltetrahydrofuran, methanol, acetonitrile, and toluene) were experimentally determined. For this a flammability apparatus was constructed, consisting of a 5.3 L spherical vessel with an exploding fuse wire as ignition source positioned at the centre of the vessel. The temperatures inside the vessel were recorded using thermocouples, and a pressure transducer monitored the pressure increase associated with the ignition of a flammable mixture. Based on the experimentally determined flammability diagrams the LOCs of the 9 solvents were thus quantified at elevated pressures and temperatures. While this study is a very valuable contribution, the solvent selection and the investigated pressure and temperature conditions are limited by operational limits of the experimental design. This serves to highlight the challenges in performing measurements at the working temperature, pressure and concentration ranges that can be adopted for industrial processes.
Partial pressure (solubility) of O2
For heterogeneously catalysed oxidations, the Henry’s law constant can be used to quantify the oxygen solubility in the liquid, which is an essential quantity for reactor design and optimization. It can be either determined experimentally or predicted based on thermodynamic equations of state.43 However, it is important to note that Henry’s law only applies when chemical equilibrium has been reached in a dilute solution (typically <1% solute concentration). Thus, care must be applied in extrapolating these values to solutions containing a synthetically-relevant amount of O2. While the solubility of O2 in aqueous solutions has been studied extensively, similar studies in organic solvents are more limited, particularly for hydrocarbons and alcohols containing more than 5 carbons.44
Process safety
Based on the discussion above, we will provide some concluding remarks on how process safety can be ensured. In general, moving from batch to continous flow improves safety as the internal reactor volume (i.e. the reactive volume) is decreased by up to 3 orders of magnitude, thus reducing the impact in case of failure.45 In addition, scaling-down also leads to increased heat and mass transfer processes, in turn reducing the risk of hot spot formation.11 Furthermore, the volumetric flow rates associated with this scale of operation allow using ancillary tubing with inner dimensions below the flame propagation threshold.46 Independent of the scale of operation, the reaction stream temperature needs to be cooled and kept below its flash point, and diluting the outlet with inert gas will avoid the formation of explosive mixtures downstream of the reactor.45 In terms of the product and exhaust streams leaving the reactor, any unreacted oxygen needs to be vented, and the use of condensers will limit the amount of evaporated solvent in the exhaust gas stream. Finally, the process control strategy needs to ensure that the temperature in the entire reactor and associated process streams is below the flash point and AIT. Thus, efficient cooling or dilution measures need to be implemented in the process.