Abstract
Herein we present a continuous flow reactor printed from stainless steel by selective laser melting. The reactor was specifically designed for a fast difluoromethylation reaction with nBuLi as base and fluoroform as atom-economic and inexpensive reagent. The reactor features four inlets to allow introduction of substrate, nBuLi, fluoroform, and a final quench solution. The reaction was completed within less than 2 min at −65 °C. The utilization of stainless steel as reactor material is critical to accomplish the heat transfer as well as the chemical and mechanical resistance that is required for this transformation.
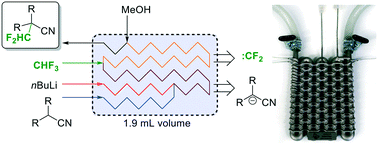
Introduction
Continuous flow micro- and milli-reactors have found increasingly wide applications in organic synthesis on all scales.1,2 The rapidly growing interest can be attributed to a range of advantages offered by these devices. Compared to traditional batch reactors, continuous flow microreactors typically exhibit enhanced heat and mass transfer, improved safety, and higher levels of controllability.1 Furthermore, multiple reaction steps, purification steps and analysis can be combined into a single continuous production unit.2,3 The flow systems are usually assembled from relatively simple, off-the-shelf components, such as polymer or metal tubings in combination with standard connectors to join these pieces together (such as those used in standard high performance liquid chromatography (HPLC) instruments).1 These components, while readily available and cheap, allow only limited design complexity for microfluidic applications. More elaborate architectures are accomplished within microreactors. Microreactors are commercially available in various pre-determined designs and from various inert materials (most commonly glass, stainless steel/Hastelloy, or silicon carbide ceramic).4 These reactors are typically manufactured by well-developed mass-production techniques, such as micromachining, laser ablation, or etching, with little possibilities for customization.4 In recent years, researchers have explored rapid prototyping technologies to construct more complex, customized microreactors.5Several structural elements, such as mixing structures, residence time channels, separation units, and interfaces for in-line analysis, have been incorporated into these devices.5 So far, the majority of these reactors have been fabricated from poly(dimethylsiloxane) (PDMS) using soft lithography.5 Soft lithography is a rather complex, multistep process which is applicable for the fabrication of planar, two-dimensional microreactors (structures with varying width but identical depth). The fabrication of more elaborate, truly three-dimensional geometries significantly increases the number of production steps and, consequently, production time. The main limitation of PDMS reactors is the low chemical compatibility with organic solvents. Furthermore, the low mechanical strength and the low temperature stability prevent applications at elevated pressures and temperatures.5 These devices, while extensively used for biochemical and analytical applications (e.g. gene sequencing and point-of-care diagnostics), have, thus, found only limited use in organic synthesis.5Compared to soft lithography, additive manufacturing (a.k.a. 3D printing) is more automated, faster, and, furthermore, allows the fabrication of reactors of nearly arbitrary complexity.6,7 For additive manufacturing, a virtual model is initially created in a 3D graphics software. This model is then used to directly build the 3-dimensional structure layer-by-layer, typically without the need for any further planning of the manufacturing process. These manufacturing techniques provide virtually full design freedom and allow fabrication of microreactors with complete control over mixing structures, mixing points, flow paths, and residence volumes. The 3D CAD file is easily shared with collaborators for examination and, additionally, can form the basis for finite element analysis and computer-assisted design optimization (Fig. 1). Despite the many advantages of 3D printing, applications for the construction of microreactors are still surprisingly rare.7–9 Most of the devices reported so far are printed by fused deposition modeling,8 and stereolithography.9 While comparatively cheap, these techniques are currently restricted to polymer-based materials which exhibit low stability against a range of reagents and common organic solvents, such as aromatic solvents, ethers and chloroform.10 Moreover, the low thermal conductivity limits applications to reactions which proceed at room temperature and do not release a lot of heat. With the emergence of high-power lasers for additive manufacturing, parts can now be printed from a variety of metals by selective laser melting (SLM).11 These materials provide the thermal conductivity as well as chemical, mechanical and thermal stability required for applications in organic synthesis.11–14 Utilization of SLM techniques for the fabrication of continuous flow microreactors have been recently reported from the laboratories of Edmondson and Christie.12 A printed reactor from a titanium alloy was coupled with online monitoring for automated optimization of two model reactions.12b Additionally, Innosyn announced customized 3D printed continuous flow reactors from metals.13 Specific applications of those reactors for synthesis have not been published so far.
Fig. 1 Workflow for fabrication of a microreactor by 3D printing. The printing process starts with a CAD-model. The data is then transferred to the rapid prototyping plant, where the model is built layer-by-layer. The digital model can be shared with collaborators and can be used as the basis for finite element simulations.
Our group has recently become interested in fast, late-stage difluoromethylation and trifluoromethylation reactions performed under scalable continuous flow conditions.15,16 The most attractive difluoromethyl-source, from an economic and environmental perspective, is fluoroform (CHF3, Freon 23). Fluoroform, a nontoxic and ozone-friendly gas (bp −82 °C), is generated as a large-volume waste-product during the production of fluoropolymers. Due to its extraordinarily low reactivity, however, it has very little current use. Only recently the first synthetically relevant transformations with fluoroform as reagent have started to emerge.17 We have become particularly interested by a difluorormethylation reaction developed in the laboratories of Mikami.18 The protocol generates difluorocarbene by a fast deprotonation of fluoroform with rapid subsequent α-elimination of fluoride. The difluorocarbene then reacts with the anion of the substrate (Fig. 2). Both reactions are exothermic and fast, even at sub-ambient temperatures. Herein we report the design and manufacturing of a millifluidic flow reactor specifically designed for this reaction. A reliable and robust reactor was produced from stainless steel by selective laser melting (SLM). The reactor features four inlets to combine the substrate feed with two reagent feeds and a final quench solution. The reaction was performed at a reaction temperature of −65 °C to generate the desired product in excellent yields after a total reaction time of less than 2 min.
Fig. 2 The difluoromethylation reaction needs four inlets and one outlet. Stainless steel is the material of choice for the reactor to provide high thermal conductivity and good chemical, mechanical and thermal stability.