Blast furnace, a vertical shaft furnace that produces liquid metals by the reaction of a flow of air introduced under pressure into the bottom of the furnace with a mixture of metallic ore, coke, and flux fed into the top. Blast furnaces are used to produce pig iron from iron ore for subsequent processing into steel, and they are also employed in processing lead, copper, and other metals. Rapid combustion is maintained by the current of air under pressure.
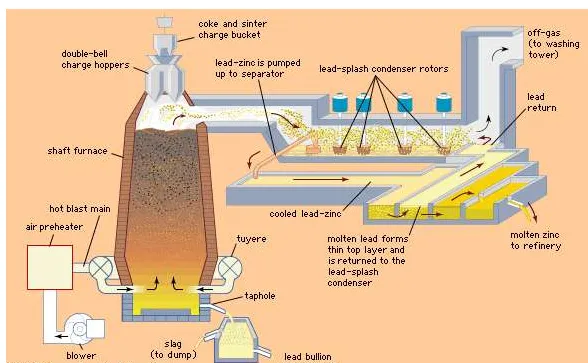
A zinc-lead blast furnace and lead-splash condenser.
Blast furnaces produce pig iron from iron ore by the reducing action of carbon (supplied as coke) at a high temperature in the presence of a fluxing agent such as limestone. Ironmaking blast furnaces consist of several zones: a crucible-shaped hearth at the bottom of the furnace; an intermediate zone called a bosh between the hearth and the stack; a vertical shaft (the stack) that extends from the bosh to the top of the furnace; and the furnace top, which contains a mechanism for charging the furnace. The furnace charge, or burden, of iron-bearing materials (e.g., iron-ore pellets and sinter), coke, and flux (e.g., limestone) descends through the shaft, where it is preheated and reacts with ascending reducing gases to produce liquid iron and slag that accumulate in the hearth. Air that has been preheated to temperatures from 900° to 1,250° C (1,650° and 2,300° F), together with injected fuel such as oil or natural gas, is blown into the furnace through multiple tuyeres (nozzles) located around the circumference of the furnace near the top of the hearth; these nozzles may number from 12 to as many as 40 on large furnaces. The preheated air is, in turn, supplied from a bustle pipe, a large-diameter pipe encircling the furnace. The preheated air reacts vigorously with the preheated coke, resulting in both the formation of the reducing gas (carbon monoxide) that rises through the furnace, and a very high temperature of about 1,650° C (3,000° F) that produces the liquid iron and slag.
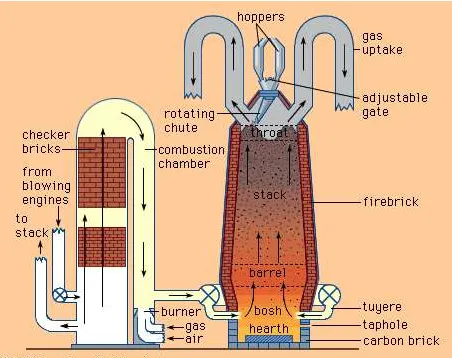
Schematic diagram of modern blast furnace (right) and hot-blast stove (left).
The bosh is the hottest part of the furnace because of its close proximity to the reaction between air and coke. Molten iron accumulates in the hearth, which has a taphole to draw off the molten iron and, higher up, a slag hole to remove the mixture of impurities and flux. The hearth and bosh are thick-walled structures lined with carbon-type refractory blocks, while the stack is lined with high-quality fireclay brick to protect the furnace shell. To keep these refractory materials from burning out, plates, staves, or sprays for circulating cool water are built into them.
The stack is kept full with alternating layers of coke, ore, and limestone admitted at the top during continuous operation. Coke is ignited at the bottom and burned rapidly with the forced air from the tuyeres. The iron oxides in the ore are chemically reduced to molten iron by carbon and carbon monoxide from the coke. The slag formed consists of the limestone flux, ash from the coke, and substances formed by the reaction of impurities in the ore with the flux; it floats in a molten state on the top of the molten iron. Hot gases rise from the combustion zone, heating fresh material in the stack and then passing out through ducts near the top of the furnace.
Blast furnaces may have the following ancillary facilities: a stock house where the furnace burden is prepared prior to being elevated to the furnace top by skip cars or a belt conveyor system; a top-charging system consisting of a vertical set of double bells (cones) or rotating chutes to prevent the release of furnace gas during charging; stoves that utilize the furnace off-gases to preheat the air delivered to the tuyeres; and a cast house, consisting of troughs that distribute liquid iron and slag to appropriate ladles for transfer to steelmaking furnaces and slag-reclamation areas.
In Europe, the blast furnace developed gradually over the centuries from small furnaces operated by the Romans, in which charcoal was used for reducing ore to a semisolid mass of iron containing a relatively small amount of carbon and slag. The iron mass was then hammered to remove the slag, yielding wrought iron. Increases in the height of the furnace, coupled with mechanical bellows for introducing greater amounts of air into it, allowed the higher temperatures needed to produce a high-carbon iron known as cast, or pig, iron. This mode of production was used in central Europe by the mid-14th century and was introduced into England about 1500. Charcoal was the only furnace fuel until the 17th century, when the depletion of forests that provided the charcoal in England led to experiments with coke, which is produced from coal. Coke had been widely adopted for use in blast furnaces by the mid-18th century, and the principle of heating air before it entered the furnace was introduced in the early 19th century.
Modern blast furnaces range in size from 20 to 35 m (70 to 120 feet), have hearth diameters of 6 to 14 m (20 to 45 feet), and can produce from 1,000 to almost 10,000 tons of pig iron daily.